锂电铜箔:被忽视的、不可或缺的锂电基础材料
铜箔在锂电池中充当负极材料载体及负极集流体,是锂电池的重要材料。锂电池严苛的工作环境与性能要求,对铜箔的厚度、抗氧化性能及粘附性能提出了多方面的要求。作为锂电池的关键原材料,铜箔的厚度、抗拉强度、伸长率、均匀性、表面性能等指标直接影响到锂电池的循环性能、能源密度等指标。
新能源汽车推动锂电铜箔进入新一轮需求高景气周期:五年三倍
新能源汽车的快速发展已经深入人心,在2020年全球新能源汽车销量达到300万辆的基准假设下,锂电铜箔(含动力电池用和非动力电池用)将从目前的7-8万吨需求量,攀升至20万吨附近。国内锂电铜箔需求量则从3-4万吨攀升至10万吨一线,占全球消费量的50%+。“五年三倍”成长空间值得期待。
供不应求或将成常态,盈利周期已然开启
相较于需求的爆发式增长,锂电铜箔生产企业明显未做好准备,供应捉襟见肘。15-16年更多是在产企业调整产品结构满足需求,但转产和弹性生产空间极其有限,随着16年下半年国内各项新能源汽车政策的明朗,锂电铜箔供需矛盾将再次被激化。
考虑到,高资本开支、长建设周期、较高市场/技术壁垒,我们预计锂电铜箔供不应求局面或将维持到2018年。锂电铜箔已经全面转向卖方市场。
而盈利周期也已经开启,从主流锂电铜箔企业毛利率水平已经从15年的13-15%攀升至23-25%。
一、锂电铜箔:被忽视的、不可或缺的锂电基础材料
按照铜箔的应用领域,可以将铜箔划分为三大品类:
1)覆铜箔层压板(CCL)及印制线路板用铜箔(PCB),普遍应用于电子信息产业,也是铜箔应用最为广泛的领域,占到了国内铜箔总产出的80%。厚度一般在12-70μm(标准铜箔),和105-420μm(超厚铜箔);
2)锂离子二次电池用铜箔,包括动力电池用锂电铜箔和非动力电池用锂电铜箔,为铜箔第二大应用领域,占到了国内铜箔总产出的13%左右。厚度一般在7-20微米(即锂电铜箔);
3)电磁屏蔽用铜箔,主要应用于医院、通信、军事等需要电磁屏蔽的部分领域。
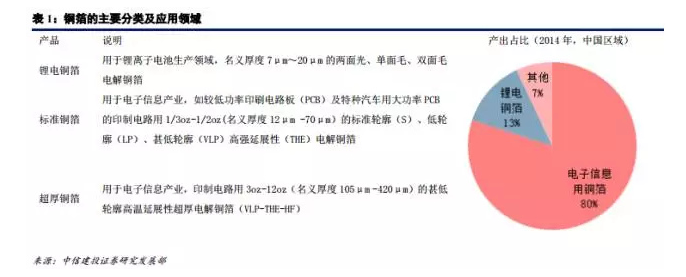
具体铜箔背景资料详见附录部分,下面我们重点论述下锂电铜箔。如图1所示,锂电铜箔是锂电池重要的基础材料之一。锂电池是利用储存在正极材料中的锂离子以及电子在充电放电过程中反向移动从而实现正常工作的,其主要结构为正极、负极和电解液。锂电铜箔在锂电池中既充当负极活性材料的载体,又充当负极电子收集与传导体:
1)锂电池一般都将负极材料(石墨)均匀地涂覆在一层极薄铜箔上,经干燥、滚压、干切等工序后,制得负极电极,在此过程中,铜箔充当了负极材料的载体;
2)而负极集流体的作用则是将电池活性物质产生的电流汇集起来,以产生更大的输出电流。集流体要具有尽可能小的内阻,且易于加工的特点。铜箔因导电性良好,质地较软,制造技术成熟,价格也相对低廉,自然而然成为锂离子电池负极集流体的首选材料。
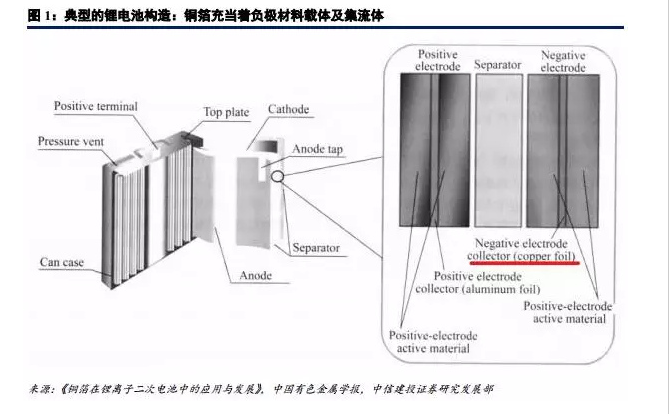
与大众认识不同,锂电铜箔有着较高的技术要求,绝非铜箔“大路货”。锂电池严苛的工作环境,对铜箔提出了多方面的技术要求,包括:
1)厚度非常小,以满足锂离子电池的高体积容量要求;通常厚度多在8-12μm之间。
2)与负极活性材料层的粘合强度高,表面能均匀地涂敷负极活性材料而不脱落;
3)化学与电化学性能稳定(抗氧化),具有良好的耐蚀性;
4)电导率高;
5)成本低,从而尽可能的降低锂电池成本。
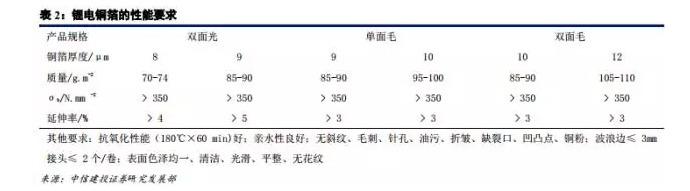
锂电铜箔的性能也对锂电池质量密切相关,铜箔是名副其实的被忽视的、不可或缺的锂电基础材料。如铜箔厚度的均匀性对电池容量和一致性会产生直接影响。
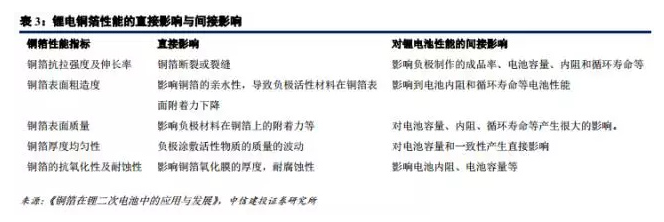
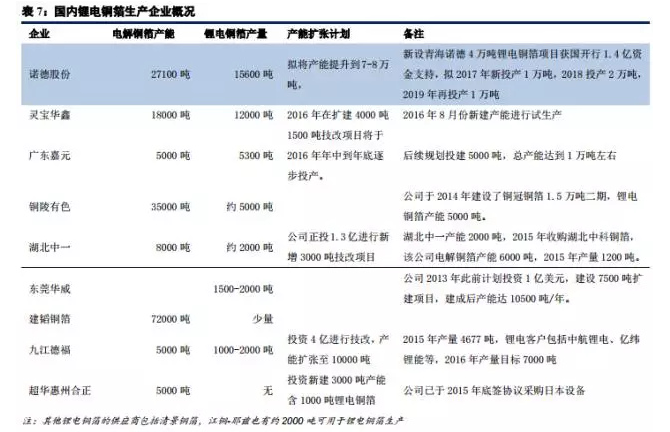
更进一步,动力电池对锂电铜箔则有着更高的要求。如上文所述,锂电铜箔又可以分为动力电池用和非动力电池用(如3C、储能等)两大品类;因新能源汽车锂电池使用量大,能源密度与循环次数要求高、工作或制造过程中,温度较高,这些对动力电池锂电铜箔也就提出了更高的要求:
1)屈服强度要求更高。新能源汽车在追求高能量密度,而使用新型负极材料时,对铜箔的屈服强度(即抵抗微量塑性变形的应力)提出了更高的要求。
2)高温稳定性要求更高。如在锂离子电池制作过程中,铜箔会被加热至200℃左右,因此要求铜箔在加热200℃时不发生软化且维持初始的屈服强度。
3)从减重、轻量化的角度出发对铜箔的厚度提出了更高的要求。尤其是纯电动汽车配备的电池单元数量比较多,仅铜箔的重量就达10 kg以上(与电池容量有关)。因此,减轻电池上铜箔的质量,降低铜箔原材料成本,同时提供高能量密度,成为对未来锂离子电池用铜箔的又一要求。要达到这一要求,当前最主要的方式是减小铜箔厚度,目前,主流锂离子电池铜箔的厚度为8~10 μm(其中,动力电池多采用8μm双面光锂电铜箔,而3C电池则可采用9μm以上或单面毛的产品)。或者采用打孔等方式降重,如日本三井金属公司开发出空隙率为50%的铜箔。
4)一致性要求更高。新能源汽车因电池使用量大,对锂电铜箔产品性能的一致性要求也就更高。
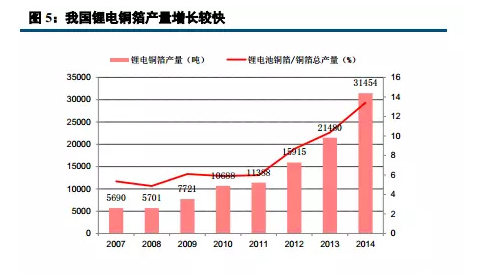
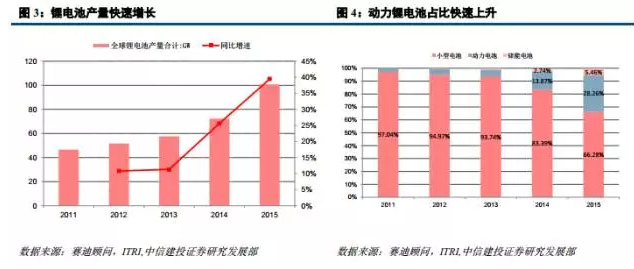
二、新能源汽车推动锂电铜箔进入新一轮需求高景气周期:五年三倍
锂电池传统上主要应用于3C产品当中,在经历了智能手机、平板电脑产品创新后,2012-2013年之后3C产品用锂电池的需求增速已经有所放缓。但在国内、外新能源汽车放量的推动下,动力电池消费需求迅速兴起,已然接替3C产品成为锂电池消费增长的主要动力--2015年,全球新能源汽车销量为73万辆,同比增长108%;锂电池产量也从2014年72GW,升至100GW,同比增长40%;动力电池在锂电池产量中的占比也由2014年的14%快速提升到2015年的28%。
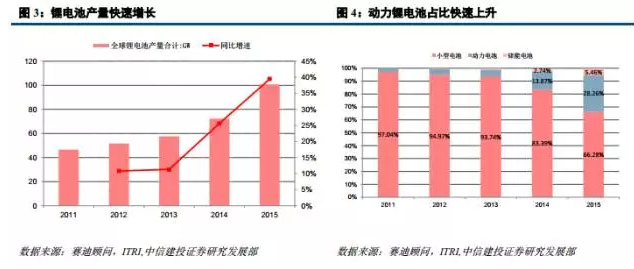
这对锂电铜箔需求的拉动是显而易见的。2014年国内锂电铜箔产量为3.15万吨,同比增长46%;初步估计 2015年锂电铜箔产量将达到3.9万吨,保持22%左右的高速增长。
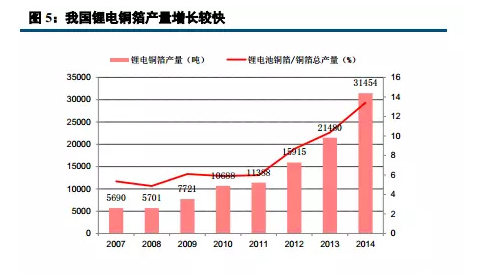
往后看,我们认为新能源汽车产业链上,有三个基准判断毋庸置疑:
1)新能源汽车快速发展毋庸置疑。在国内、外补贴优惠政策的推动,民众节能减排意识及对新能源汽车认识不断深化的影响之下,国内、外新能源汽车的产销增速仍将保持快速增长势头。我们预计,2016年国内新能源汽车的产销量将达到67万辆(增长80%),而全球的产销量水平将上升到110万辆以上;2020年全球新能源汽车将突破300万辆。2016年下半年,随着国内骗补调查进入尾声,地方补贴政策趋于明朗,新能源汽车的销售也或将拾级而上。
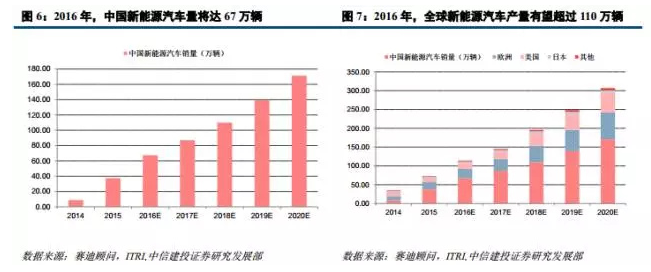
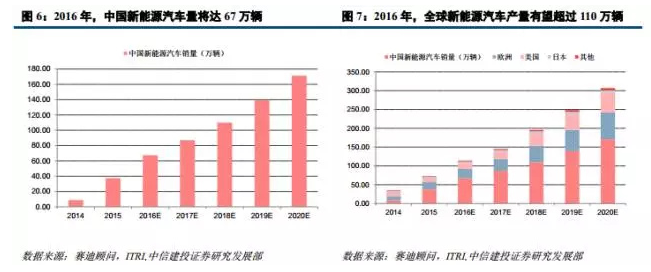
2)新能源汽车动力电池将继续推动锂电池需求的快速增长。2014年新能源汽车锂电池需求为11GW,2015年在我国新能源汽车大幅增长的驱动下,动力锂电池需求增长至25GW;我们预计新能源汽车的持续增长将使2016年动力锂电池的需求上升至42GW,年增长率达70%。以动力锂电池为核心驱动力,2016年全球锂电池的需求量将达到120GW附近。
3)动力电池用锂电铜箔需求的快速增长也毋庸置疑,将从2015年的2万吨增长至2020年的10万吨。2014年动力电池用锂电铜箔需求量仅为1万吨左右,2015年这一数值为2万吨。锂电池中负极集流体铜箔用量大约为2-3.5g/Ah,考虑材料使用率,按平均3g/Ah,假设电池输出电压为3.6V,进行计算可以得到(即也可以理解为度电所需铜箔为0.83公斤),2020年全球新能源汽车动力电池用铜箔的使用量将达10.5万吨。计入非动力电池用锂电铜箔后,全球锂电铜箔将从2015年的7-8万吨,增加至20万吨。
国内锂电铜箔需求量的占比也将从2014年的39%升至2020年的54%。按照我们的测算,国内锂电铜箔需求量将从2015年的3-4万吨增加至2020年的10万吨;其中,动力电池用锂电铜箔需求量将从2015年的1.3万吨飙升至2020年的6.2万吨。
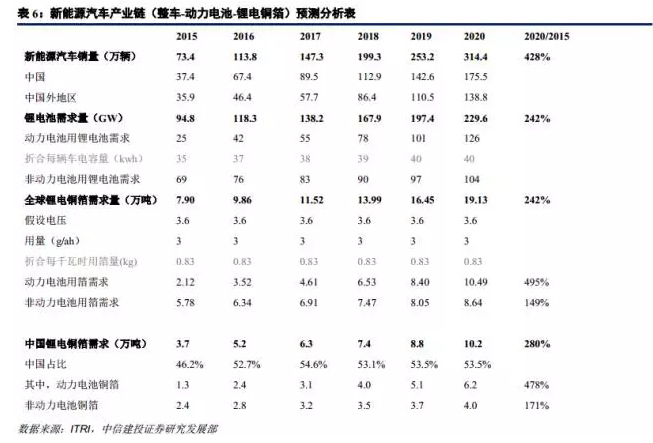
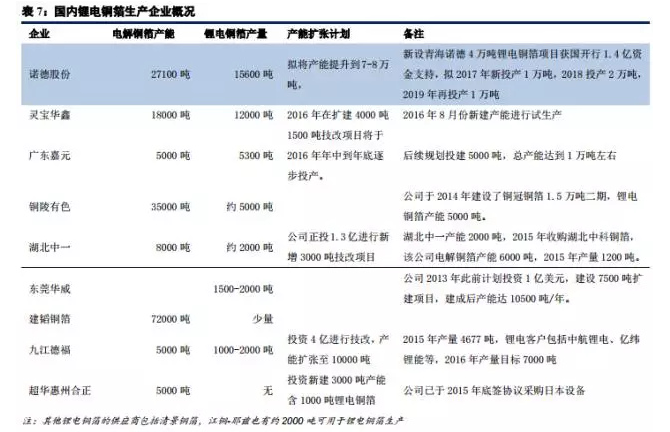
1)锂电铜箔新建产能建设周期长、投资规模大同样是限制产能释放的客观原因,2018年才可能迎来第一轮投产高峰。按照主流生产企业的投扩建信息,新建项目每万吨投资规模在6-7个左右(若采用国内设备,至少也需要5个亿)。同时,由于铜箔生产需要大量的基建工作,管路工程较大,建设周期通常较长,新建产能的建设周期大约需要18-24个月,考虑到投产和达产的过程,达产需要的时间可能会更长。而按照目前已经在规划的投产项目来看,2018年才会迎来第一轮投产高峰,并且集中在诺德股份一家企业。

2)与此同时,由PCB铜箔转向生产锂电铜箔,或者新进入到锂电铜箔行业,企业会面临技术与市场两大壁垒,产能的投放或许更长的时间:
a.在技术壁垒方面,锂电铜箔的生产技术是一种以经验积累为主的制造技术,需要通过长期的生产实践摸索、总结与创新才能获得,如复合添加剂的制备技术、生箔技术、后处理技术等,均无法通过简单复制被新进生产厂商所掌握。锂电铜箔的技术含量高,对生产工艺与设备的要求严格。国内新进厂商需具备自行设计、加工高档电解铜箔生产的关键设备的能力,同时在购置该等关键设备时则需要具有非常充足的资金实力。国内现有的锂电铜箔生产企业,在实现批量化供应锂电铜箔之前都经历了1-2年(甚至更长)的产能建设及产品开发过程。
b.在市场壁垒方面:锂电铜箔的质量对于锂电池的性能有着直接的影响,锂电池企业,特别是动力电池企业,对供应商有着较为严格的供应认证体系,对于新从事锂电铜箔生产的企业来说,通过认证、试样、再到大批量供应需要较长的时间。
c.资本壁垒也比较强:即进入锂电铜箔行业,企业不但需要大规模的资本开支,同时对现金流的要求也非常高,通常需要现金支付上游铜线原料,下游可能会被电池企业拖欠帐期。
综合来看,我们认为2016年锂电铜箔的供需矛盾将进一步激化,行业整体供给不足或将延续到2018年。锂电铜箔将迎来一轮为期2-3年的“超级周期”!这一点,其实在各主流生产企业2016年一季报中得到了体现,锂电铜箔已经成为卖方市场,加工费水平水涨船高(在过去一个季度加工费平均上调了2000-3000元/吨),主流锂电铜箔企业的盈利能力飙升,我们判断行业平均毛利水平在1.5万元/吨左右,正常生产经营企业的平均单吨净利应该在0.5万元/吨。而随着供给进一步紧张,加工费不排除进一步上调的可能,行业盈利能力也将进一步抬升。
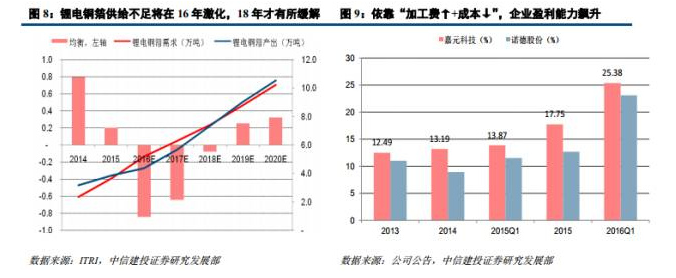
综上所述,我们认为在新能源汽车的推动下,锂电铜箔将迎来一轮为期2-3年的“超级周期”,建议积极把握“锂电铜箔超级成长周期”带来的投资机遇,可重点关注诺德股份、铜陵有色,并建议投资者根据自己的投资偏好选择相应的投资标的。具体上市公司对比分析参见下表:
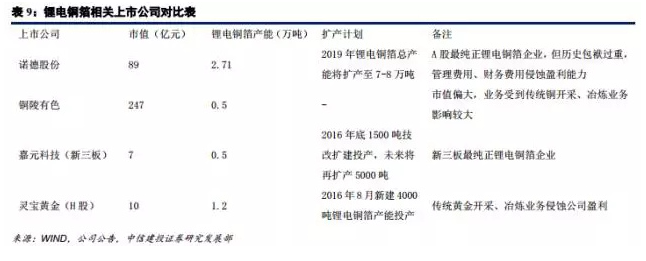
铜箔是电子、电池工业的基础原材料。业界一般将采用压延、电解、溅射等方法形成一定厚度以下的铜带(片)称为铜箔。美、日等国多以0.1mm作为区分标准,0.1mm以下的为铜箔。在我国,铜箔指横断面呈矩形,厚度均一并等于或小于0.15 mm 的轧制(压延)或电沉积产品。近几年铜箔技术水平的发展,铜箔和铜带的界限变得模糊起来,电解与压延铜箔的使用界限变得模糊起来。例如,超厚铜箔(指标称厚度在3 oz-14 oz(105um~500um)的铜箔)虽然压延法生产难度较大,但已经有电解铜箔企业可以生产出超厚铜箔了。
铜箔的应用领域:铜箔不仅是制造CCL及PCB的重要基础材料,而且在其它领域也具有广泛应用,主要有锂离子电池负极载体、等离子平板显示器用屏蔽材料、热敏电阻、太阳能背板、散热材料等。
铜箔按照制备工艺不同可以分为压延铜箔和电解铜箔。铜箔的制备工艺经历了“压延-电解-电解压延互补”的过程。最初,各厂商的产品主要以压延铜箔为主。后来,由于压延铜箔在幅宽上的限制,难以满足需求,逐渐被电解铜箔所替代。近几年,随着电子产品的发展对铜箔的功能提出了更高的要求,压延铜箔又逐渐因为其自有的特性而有了生命力。
a.压延铜箔,是将厚铜板加热到退火温度,然后进行轧制,退火和轧制重复多次,制成达到厚度要求的原箔。然后根据使用要求对原箔表面进行处理,最终制备得到符合使用要求的铜箔。压延铜箔生产工艺复杂、流程长、一次性投入高、成本高,铜箔的极限厚度也受轧辊限制,优点是采用压延方法生产的铜箔一般具有较好的性能。
b.电解铜箔是以硫酸铜溶液为原料,在以不溶性材料为阳极、底部浸在硫酸铜电解液中恒速旋转的阴极辊为阴极的电解槽中进行电解,溶液中的铜沉积到阴极辊筒的表面形成铜箔,铜箔的厚度由阴极电流密度和阴极辊的转速所控制。待铜箔随辊筒转出液面后,再连续地从阴极辊上剥离,经水洗、干燥、卷取,制成原箔。在此基础上对原箔进行后续处理得到最终铜箔。电解铜箔工艺复杂,但是成本较压延铜箔低,产品厚度也较易控制。
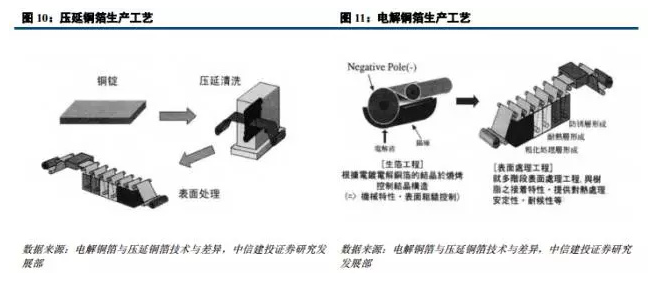
c.压延铜箔、电解铜箔,各有优劣。压延铜箔以物理锻造法制造原箔,而电解铜箔以电化学沉积法制造原箔。通过不断的轧制,压延铜箔通常具有更好的物理性能,如铜的纯度要高,并具有列优异的强度、韧性和抗弯曲性能,弹性系数/致密度/延展性要高。但电解铜箔的这些物理性能,特别是弯曲性能要差。压延铜箔的厚度与宽度会受到轧辊尺寸的限制,电解铜箔的尺寸约束更少。在成本方面,压延铜箔的固定资产投产较大,而且生产成本较高,电解铜箔在成本方面具有优势。在生产技术方面,压延铜箔的生产技术要求高,工艺复杂、流程长,同时,生产技术多掌握在日本、美国企业手中,生产多有专利限制。
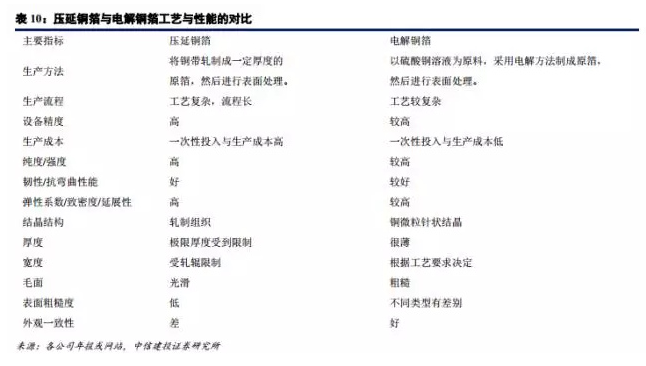
目前世界铜箔的发展,整体格局还是以电解铜箔为主,压延铜箔为补充。大致经历了“压延--电解--电解压延互补”的过程。在覆铜板最初生产时期,世界上大多数都是使用压延铜箔。后来由于它在幅宽上的限制,难以满足大尺寸覆铜板的生产需要,且成本较高,从上世纪60年代末至70年代初开始,压延铜箔逐渐被电解铜箔所替代。近几年,可携式电子产品的普及,对高频高速化、薄型化、功能化产品提出更高的要求,压延铜箔由于其自有的特性,其重要性又凸显了出来。但即便如此,压延铜箔的产值和电解铜箔相比也不在再一个量级上。
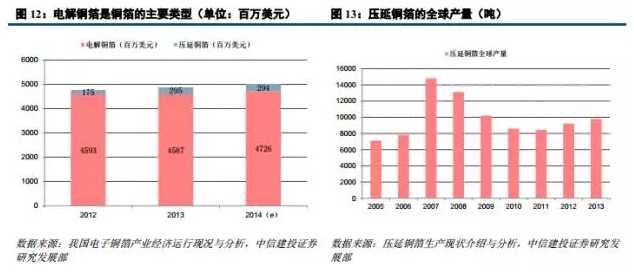
全球压延铜箔的产量回升。由于其制造难度以及在高端产品中的应用,其产量跟电解铜箔也没法比较。世界用于PCB的压延铜箔在2013年产销量达到9780吨,比2012年增加了5.9%。2012年世界压延铜箔的产量达到了9230吨,全年产值达到2.89亿美元,比2011年增加了9.2%。对2012年全球压延铜箔产量进行分析,厚度18微米铜箔占市场比例最高为76%,其次是12微米的占15%,35微米的占9%。目前对薄规格(如6微米,8,10等)压延铜箔需求不大。
高精压延铜箔主要集中于国外厂商。由于高精压延铜箔的技术门槛较高,所以全书主要的压延铜箔集中于几家厂商:NipponMining(日矿)、Fukuda(福田金属)、Olinbrass(美国奥林)和Hitachi Cable(日立电线)等。可以看出,压延铜箔领域,日企的水平处于领先地位。
国内压延铜箔需求主要通过进口来满足,国内压延铜箔企业正在起步。经过数年的摸索、大规模的设备引进之后,国内的压延铜箔生产企业正在突破压延铜箔的壁垒。2014 年在中国的企业(包括外资企业)还产销压延铜箔282 吨(约有90 吨用于FPC中)。到2014 年底,国内已有中铝上海铜业、苏州福田、山东天和、灵宝金源朝辉等四个厂家的压延铜箔已形成产能,总产能达到1.14 万吨,但产出有限。在国内供应能力不足的情况下,国内压延铜箔的需求主要通过进口来满足。
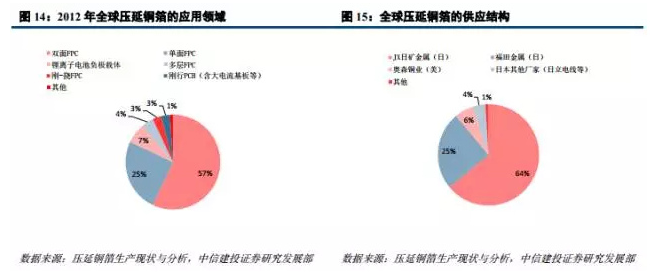
压延铜箔主要应用于覆铜板、锂电池行业。
a.压延铜箔最大的最直接的应用市场是挠性覆铜板(FCCL)制造业,最大的间接应用市场是挠性改制电路板(FPC)。挠性覆铜板制造业需求的压延铜箔量,约占整个压延铜箔产销量的82%(其中双面FPC占57%,单面FPC占25%)。
b.锂离子电池负极载体领域的压延铜箔占整个压延铜箔使用量的7%左右(2012年)。由于锂离子电池市场在近两年扩大,这一压延铜箔的市场比例比前几年有所提高(2009年的4%、2010年的6%)。 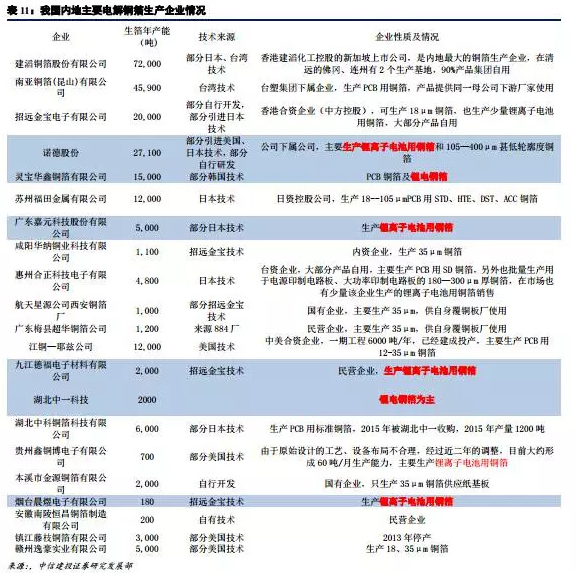